Fluid Separations
Heat Transfer and Fluid Separation in the Energy Transition
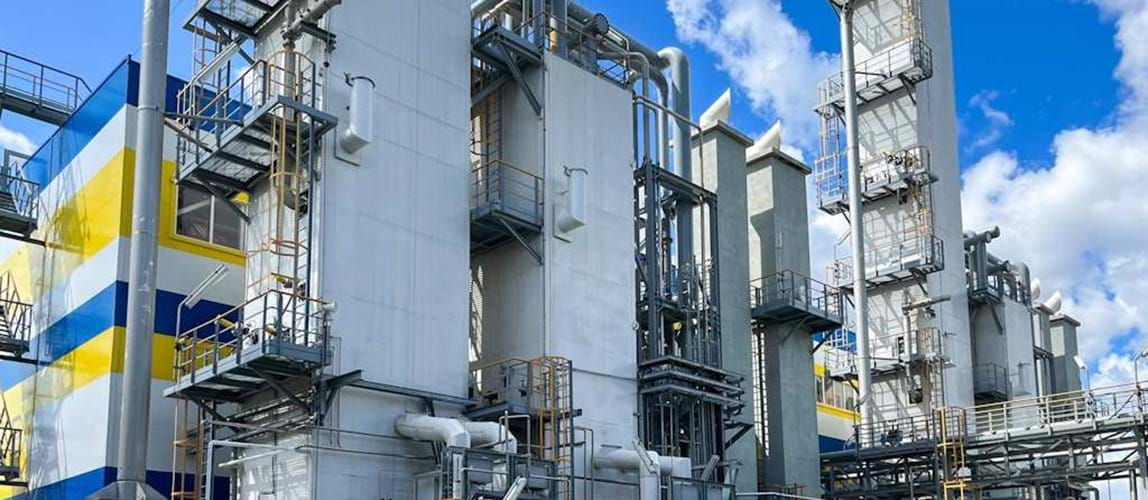
- Date From 28th March 2025
- Date To 28th March 2025
- Price From £15.00.
- Location Nunn Hall (Room 421), IOE, 20 Bedford Way, University College London, Faculty of Education and Society, WC1H 0AL
Overview
This is an exciting new one-day event, organised by IChemE’s Fluid Separations Special Interest Group and the Heat Transfer Society.
Industry leaders, experts and academics will explore the vital role of heat transfer and fluid separation technologies for energy transition.
Presentations, mainly from industry experts, will focus on producing and using hydrogen and ammonia, applying electric furnaces, carbon capture, heat exchanger innovations, applications of digital twins and technology scaling for energy transition.
The event promises insights, networking opportunities and inspiration for all - from early-career engineers to seasoned professionals.
Participants are also invited to attend the Heat Transfer Society's Annual Dinner afterwards at the Grand Connaught Rooms, Covent Garden, London.
Speakers
Vincent White, Principal Research Associate, Air Products
Presentation: Progressing the Energy Transition through transformative hydrogen projects
For energy-intensive sectors of the economy, hydrogen is a solution to the challenge of decarbonisation. Air Products has made a commitment in first-mover hydrogen projects, leading the industry with a portfolio of technologies and expertise to ensure the future climate benefits generated by these projects come online at a crucial moment in the energy transition.
Today, almost all industrial-scale hydrogen is produced using Steam Methane Reforming technology. In this presentation Air Products will describe our announced projects in renewable and low-carbon hydrogen. These projects are designed with the next generation of hydrogen production technologies, from reforming with CO2 capture to electrolysis of water. Over 10 years ago Air Products successfully retrofitted an SMR facility with our novel CO2 VSA carbon capture technology in Port Arthur, Texas, demonstrating that over 90% of CO2 from process syngas can be cost-effectively captured.
Building on our success in low-carbon hydrogen production, our recently announced hydrogen project in Louisiana, USA is designed to extend that capture rate to 95% of total production emissions using Partial Oxidation technology with CCS. The project will produce blue hydrogen for injection into Air Products’ 700-mile long pipeline on the US gulf coast and blue ammonia for export to global hydrogen markets.
In addition, Air Products’ Net-Zero Hydrogen Energy Complex in Edmonton, Canada will use Autothermal Reforming technology to achieve 90% capture and will also include a 100% hydrogen-fuelled power generation unit resulting in clean power without the indirect emissions associated with grid power.
Stepping beyond fossil fuel-based hydrogen production, Air Products is a partner in the NEOM Green Hydrogen project presently under construction in Saudi Arabia, which is designed to produce carbon-free hydrogen in the form of green ammonia to be used as an efficient hydrogen carrier for transportation globally.
Jonathan Peters, Senior Process Design Engineer, Boustead International Heaters
Jonathan graduated Loughborough University 2017 with master’s degree in chemical engineering (1st class honours). Three years cumulative experience in the Nuclear sector. Primarily involved with waste management and decommissioning activities at Sellafield site in the UK.
Current role is Senior Process Engineer at BIH. Total of six years at BIH, specialising in fired heater and waste heat recovery unit design. Chartered status with the IChemE since 2024.
Presentation: Hydrogen Firing in Fired Heaters
The presentation gives an overview of fired heaters and the general working principle. This is followed by a review of the contrasting performance when firing 100% Hydrogen (an higher hydrogen fuels) when compared to more established fuels such as natural gas and/or refinery fuel gas.
This summary includes impact to burner performance/emissions, mechanical considerations as well as control and safeguarding implications.
Agustin Valera-Medina, Director Net Zero Innovation Institute, Cardiff University
Agustin has participated as PI/Co-I on 33 industrial projects with several multi-nationals (>£35M). He has published 230 papers (h-index 42), 98 of these specifically concerning ammonia power.
He is currently PI of various projects (SAFE-AGT, FLEXnCONFU, MariNH3, OceanREFuel, CAIPIRINH3A, etc.) to demonstrate ammonia power in turbine engines, ICE, boilers and furnaces. He has supported two Royal Society Policy Briefings related to the use of ammonia as energy vector, and he is the principal author of the book “Techno-economic challenges of ammonia as energy vector”.
He is Co-Director of the Institute of Net Zero Innovation and Director of the Centre of Excellence on Ammonia Technologies (CEAT), Cardiff University. He is a Fellow of the Learned Society of Wales (2024).
Presentation: AMBURN - Ammonia for Rural Locations
Currently ~4.5 million tonnes of oil are consumed in the off-mains industrial market annually in the UK. These energy intensive processes contribute to point source emissions of 14.2 MtCO2/y.
Businesses and industries in these locations often cannot rely solely on electricity to satisfy their process heating requirements. Decarbonisation of these sites therefore presents a significant and pressing challenge. Therefore, th Amburn project will develop and demonstrate a 1 MW ammonia-fed steam boiler to help decarbonise off-grid businesses across the UK.
Funded by the Department for Energy Security & Net Zero as part of the UK Government’s £55m Industrial Fuel Switching Competition, Flogas Britain and Cardiff University will prove that ammonia is a viable, cost-effective renewable fuel for large energy users off the mains gas grid.
Phase 2 of Amburn will build upon the main findings outlined in the feasibility study of Phase 1, further developing the design of Amburn, conducting two stages of testing to enable a scale up of two orders of magnitude throughout the project, and finally carrying out a demonstration at a real customer site.
Ken Lawson, Sabic
Ken graduated from Teesside Polytechnic in 1988 as a chemical engineer and from Middlesex University 1995 with a DMS in Business Administration. Ken began his career in 1988 as a process engineer with Bechtel London working on EPC projects whilst specializing in fluid flow modelling.
In 2001 Ken joined Huntsman Teesside (formerly ICI), which became SABIC in 2007. Until 2014 Ken proposed and was involved with all aspects of design through to operation of the world’s largest Low Density Polyethylene Plant.
Since 2014 Ken has worked on SABIC’s Oil to Chemicals program, including the development and potential deployment of the electric cracking furnace. Ken has patents in the fields of chemicals from renewable energy, hydrocracking and micro injection molding.
Presentation: Technology demonstration of electric cracking furnaces - A BASF, SABIC and Linde joint development
Ethylene is one of the largest volume chemicals manufactured today and demand is anticipated to continue to grow in the coming decades as the World’s population grows and global affluence related consumption increases.
Steam Cracking is an endothermic process, requiring significant energy that is presently derived from fossil fuel combustion, resulting in significant greenhouse gas emissions.
Edward Ishiyama, Senior Technical Lead, SmartPM - HTRI
Edward is a senior technical lead for SmartPM at HTRI. He began his industrial career in 2005 as an intern at Ceylon Glass Company in Sri Lanka, where he focused on optimising furnace and air preheater operations.
He later earned a PhD in chemical engineering from the University of Cambridge, UK. His doctoral research, Modelling of Heat Exchanger Networks Subject to Fouling, led to the development of a globally adopted software tool for managing fouling in heat exchanger networks.
With extensive experience in heat transfer, process control, and thermodynamics, Edward specializes in diagnosing and solving challenges in heat exchangers and their associated networks. He also serves as the Secretary of the biennial Heat Exchanger Fouling & Cleaning Conference.
Presentation: Role of Furnace Digital Twin Models to Assess Alternative Fuel Combustion and Emissions in Practical Applications
Marco Gutarra, Global Application Manager, Alfa Laval
Marco is a mechanical engineer who began his career at Alfa Laval in 1995. For the past 10 years, he has been based in the company's central offices in Copenhagen, currently serving as the Global Application Manager for gasketed plate heat exchangers.
He specialises in supporting carbon capture projects globally, covering heat exchanger applications in CO2 capture, compression, and liquefaction systems. In addition, he provides technical and commercial expertise for the steel, pulp and paper, and inorganics industries, assisting Alfa Laval sales offices worldwide in optimising thermal solutions for industrial and sustainability-focused processes.
Presentation: CO2 amine absorption (CAPEX+OPEX) through efficient heat transfer. Enhancing Amine Carbon Capture: Cutting Costs & Boosting Performance with Heat Exchangers
Peter Drögemüller, Research and Development Manager, Calgavin
Peter has a PhD in chemical engineering, and has over 20 years of experience in heat transfer enhancement. He initially joined CALGAVIN® in 1998 as a process engineer and returned in 2003 as Research & Development Manager. He leads new product design and research on tube-side heat transfer in single and two-phase flow applications. He oversees state-of-the-art research facilities and collaborates with UK and European institutions. He played a key role in developing hiTRAN.SP design software and integrating it with industry tools. A Visiting Senior Research Fellow at UoB, he actively supports academic contributions to product development and has published extensively.
Presentation: The Role of Heat Transfer Enhancement in Absorption-Based CO2 Capture
Optimising heat exchangers in thermal processes is an important aspect for achieving net-zero emissions, particularly in the context of carbon capture, where economic viability is key to widespread adoption. Absorption-based carbon capture, primarily using amine-based chemical solvents like monoethanolamine (MEA), represents the current benchmark for capturing CO2 from flue gases, with a technology readiness level of 9. Large-scale projects utilising this approach are advancing toward final investment decisions.
Amine solvents possess properties that make heat transfer enhancement technologies especially attractive. For example, their dynamic viscosities frequently result in low-turbulent, transitional, or even laminar flow regimes when applied on the tube side of heat exchangers. This creates opportunities for employing advanced heat transfer enhancement solutions, such as hiTRAN inserts, to improve system performance. This presentation highlights case studies demonstrating the benefits of tube-side enhancement, including significant reductions in equipment and operational costs. Additionally, the use of this technology in amine air coolers is shown to lower CO2 emissions significantly. Retrofit applications of hiTRAN in existing equipment are also explored, showcasing its potential for enhancing efficiency and sustainability in carbon capture systems.
Frank Schmitter, Product Line Director Desublimators, Kelvion
Frank graduated from Ruhr Universität Bochum (RUB) in 1989 as mechanical engineer and in 1997 from Fernuniversität Hagen as economic engineer. Research and development engineer from 1990 until 1995 at RUB (Institute for Thermo and Fluid Dynamics) with specialisation in heat and mass transfer as well as fluid dynamics.
Joined GEA (now Kelvion) in 1996 as project engineer for different applications. From 2004 until 2011 the head of the desublimator department of GEA in Germany including design and manufacturing of desublimators and equipment for Phthalic Anhydride Plants.
After relocation of the manufacturing workshop in 2011 until today product line director responsible for the desublimator business as well as equipment for PA plants worldwide. Since 2014, highly focused on carbon capture by desublimation as new application for Kelvion desublimators. Co-inventor of a patented new type of desublimator for high pressure applications in cryogenic environments.
Presentation: Desublimation for Carbon Capture
Desublimation is a not widely known but is used as a separation method for gas mixtures. However, at KTS, desublimation is a well-established process for which we have been delivering equipment for more than 60 years for several applications.
This successful history started in the 1950’s with the separation of phthalic anhydride as a product from a gas phase reaction. During the last few decades, we have been expanding the range of application, finding new substances which can be separated using desublimation. Carbon dioxide is one of these applications, for which we have not only carried out a deep theoretical work with universities and well-renowned international institutes, but also, we have delivered desublimators for a full-scale pilot plant where our desublimators achieved the stringent requirements of the customer.
We will present the results of this theoretical work, as well as the outcomes of the pilot plant.
Niccolo Le Brun, Head of Digital Innovation, Hexxcell Ltd
Niccolo is the head of digital innovation at Hexxcell Ltd where he is responsible for the development of Hexxcell Studio™ Hybrid-AI Platform. His main area of expertise is the development and application of optimisation algorithms for improving processes profitability and decrease carbon emission.
Before joining Hexxcell 4 years ago, he worked for GE Hitachi as a nuclear engineer and for Imperial College London as academic researcher. His academic interests focused on working alongside major energy and retail companies to decarbonise their operation using optimal scheduling and control.
He is the co-author of over 30 publications between journal and conference contributions in the field of energy processes and systems.
Presentation: A system-level, hybrid-AI digital twin approach to optimising heat exchanger cleaning in separation units with heat recovery
Many operations in chemical engineering, particularly in oil and gas, involve the use of thermally based separation units, such as distillation columns. These unit operations almost always include some form of heat recovery, as operational costs are largely energy-driven; thus, the more heat that can be recovered, the less energy input is required. As such, heat exchangers play a crucial role in the economic performance of these units.
However, fouling is a major issue in heat exchanger operation. As heat exchangers accumulate fouling, their heat recovery efficiency decreases, leading to increased energy costs and higher carbon emissions. Excessive fouling can eventually compromise the separation unit’s performance, sometimes requiring a reduction in feed flow rate. Heat exchangers can be cleaned to restore heat recovery capacity, but these cleanings can be costly and often necessitate shutting down the unit for several days, leading to production losses.
Optimising the cleaning schedule for heat exchangers, especially the preheaters within the separation unit, is a critical step to maximise economic efficiency. There are various methods to achieve such optimisation. In this work, we present the results of applying a hybrid-AI digital twin to model both the heat exchangers and the separation unit (a distillation column) to determine an optimal cleaning schedule.
This study highlights the importance of a system-level approach that considers the close coupling between heat recovery and separation units, achieving significant cost savings.
Matthew Turnbull, Senior Advisor, BP
Matt is a chemical engineering senior advisor at BP and part of the leadership of their Fuels and Low Carbon Technologies team, based in Hull. He’s particularly interested in overcoming the real and perceived barriers to deployment of new technologies at scale and the use of chemical engineering science to solve operational challenges.
In his twenty years with bp, Matt has worked in process technology development from discovery to commercialisation. This has included syngas chemistries, biomass conversion and use of novel bio-feedstocks.
Presentation: Scaling new technologies for the energy transition
The ‘valley of death’ between research and adoption at scale for disruptive technologies continues to challenge both start-ups and major organisations. Technology readiness levels were developed in NASA, in part to bridge a gap “between the intended and actual proof of readiness” (Sadin et al., Acta Astronautica Vol. 20, pp. 73--77, 1989). Since then, variations on the theme of the readiness levels have proliferated. They are used for eligibility for research funding and government grants, and piloting is a major use of funds for start-ups. Is building something bigger always the right answer, and what alternatives are there?
The material presented at this event has not been peer-reviewed. Any opinions are the presenter's own and do not necessarily represent those of IChemE or the Fluid Separations Special Interest Group. The information is given in good faith but without any liability on the part of IChemE.
Back to events